Discover the Art and Science of Kiln-Formed Glass: A Guide for Artists and Crafters
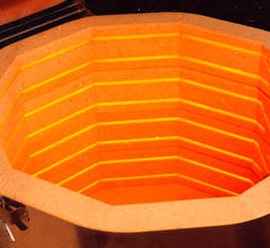
Kiln-formed glass is a fascinating and versatile medium that has been gaining popularity among artists, crafters, and hobbyists in recent years. Whether you are a seasoned professional or a beginner just starting to explore the world of glass art, this guide will give you a comprehensive overview of what kiln-formed glass is and how it can be used to create stunning works of art.
What is Kiln-Formed Glass?
Kiln-formed glass, also known as kiln-casting or kiln-fusing, is a process of melting and shaping glass using high heat and controlled cooling. Unlike traditional glass-blowing techniques, which require the use of a blowpipe, kiln-formed glass allows for greater control and precision in shaping the glass. This makes it a popular choice for artists who want to create intricate designs, textured surfaces, and complex layered effects.
The kiln-forming process begins by cutting and arranging pieces of glass into a design. The pieces are then placed into a kiln, where they are heated to high temperatures, typically between 1450°F and 1500°F. The heat causes the glass to soften and begin to flow, allowing the pieces to fuse together. Once the desired shape has been achieved, the kiln is cooled at a controlled rate to prevent the glass from cracking.
Applications of Kiln-Formed Glass
Kiln-formed glass is used in a variety of applications, ranging from functional items such as dishes, vases, and jewellery, to decorative pieces such as wall hangings and sculptures. The versatility of the medium makes it a popular choice for artists and crafters, who can use it to create unique and imaginative pieces that showcase their creativity and skills.
Some popular applications of kiln-formed glass include:
- Jewellery: Kiln-formed glass is often used to create unique and stunning pieces of jewellery, such as pendants, earrings, and bracelets. The controlled environment of the kiln allows for precise shaping and layering of the glass, resulting in beautiful and intricate designs.
- Decorative Pieces: Kiln-formed glass is a popular choice for creating decorative pieces, such as wall hangings, sculptures, and other artworks. The ability to layer and fuse different colours and textures of glass makes it possible to create intricate and eye-catching designs that can add a touch of beauty and elegance to any room.
- Functional Items: Kiln-formed glass is also used to create functional items, such as dishes, vases, and bowls. The durability and heat resistance of kiln-formed glass make it ideal for use in the kitchen and home, provided that the artist has ensured that the elements and/or colours used are safe to use as serving vessels for food.
Tips for Successful Kiln-Forming
Kiln-forming glass is both an art and a science, and there are many factors that can impact the outcome of a project. Here are a few tips for success:
- Choose the right type of glass: Different types of glass have different properties, such as melting temperature, expansion rate, and viscosity. It is important to choose the right type of glass for your project, depending on the desired effect and the conditions of the kiln.
- Experiment with colours and textures: Kiln-formed glass allows for a wide range of creative possibilities. Experiment with different colours and textures of glass to discover the effects that can be achieved through layering and fusing.
- Pay attention to kiln temperature and timing: The temperature and timing of the kiln are critical to the success of a kiln-formed glass project.
Cold working glass
- Sandblasting:
Sandblasting can be used to create intricate patterns on the surface of the glass, leaving an etched design. It can also be used to give different textural qualities to a piece of glass. There are many effects that can be created using sandblasting.
- Grinding and polishing:
Sometimes an artist will be happy to produce works that may perhaps not have exactly square or rounded edges, which is a part of the kiln-forming process as the glass melts or slumps into a mould.
However, others will painstakingly cold work the pieces to ensure that they are of a significantly high quality. This requires the use of either hand finishing or machine finishing the pieces, trimming off unwanted ‘wobbly’ edges and working through a variety of grits to gradually bring the trimmed edges to a nice polished finish. It can also mean grinding in a stopper for a perfume bottle, for instance, to achieve an air-tight fit.
- Choose the right type of glass: Different types of glass have different properties, such as melting temperature, expansion rate, and viscosity. It is important to choose the right type of glass for your project, depending on the desired effect and the conditions of the kiln.
- Experiment with colours and textures: Kiln-formed glass allows for a wide range of creative possibilities. Experiment with different colours and textures of glass to discover the effects that can be achieved through layering and fusing.
- Pay attention to kiln temperature and timing: The temperature and timing of the kiln are critical to the success of a kiln-formed glass project.
Leave a comment